潮州市定制紫外线消毒灯厂家
发布时间:2022-11-07 00:42:19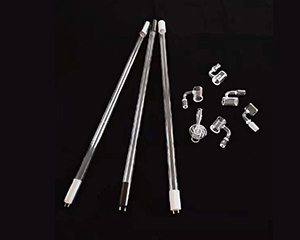
潮州市定制紫外线消毒灯厂家
1、石英是一种晶体,而玻璃则是非晶体。非晶体各向同性,而晶体的光学性能是具有方向性的,即有的方向折射率大,有的方向折射率小,这使得晶体材料不能用来作为光学材料来使用。玻璃是非晶体,而石英是晶体。非晶体各向同性,晶体的光学性能是有方向性的——有的方向折射率大,有的小——这就决定了晶体材料不能用来做光学材料。2、耐热程度不同。英管的软化点温度约1730℃,可在1100℃下长时间使用,短时间使用温度可高达1450℃ 除氢氟酸外,石英管几乎不与其他酸类物质发生化学反应,其耐酸能力是陶瓷的30倍,不锈钢的150倍,尤其是在高温下的化学稳定性,是其他任何工程材料都无法比拟的。石英玻璃的热膨胀系数*小,能承受剧烈的温度变化,将石英管加热至1100℃左右,放入常温水中也不会炸裂。玻璃管是普通玻璃做的,硬度、透明度,耐高温性、耐磨性都要差很多。3、电绝缘性能好。石英玻璃的电阻值相当于普通玻璃的一万倍,是非常好的电绝缘材料,即使在常温下也具有良好的电性能。
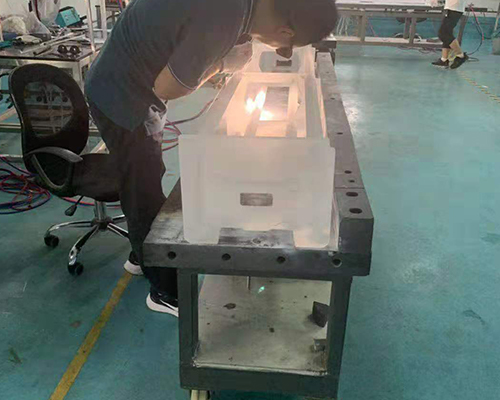
潮州市定制紫外线消毒灯厂家
中国建筑材料研究总院教授级高工石新勇、陈璐、王睿、吴洁、孙云蓉等专家撰写的《我国工业玻璃与特种玻璃标准体系现状分析及展望》文章指出:我国石英玻璃标准现状,该领域共有29项标准,产品标准20项(国家标准1项),方法标准9项(国家标准5项),另有4项新产品标准列入2008年行业标准制订计划。2008年是石英玻璃标准复审的高峰期,有12项标准得到修订。随着我国经济的快速发展,一些玻璃新品种、新技术已经形成和正在进行产业化,资源再生利用、节约能源、保护环境方面的产品日新月异,我国已开始对低温喷涂玻璃、无铅封接玻璃、防微波辐射玻璃、电磁屏蔽玻璃等产品进行科研研究和应用推广,计划根据进展情况,尽快将成熟的产品纳入标准。新产品的纳标,能够优化我国工业玻璃与特种玻璃品种结构。石英玻璃器件有三大类:第一类是石英玻璃仪器,有分馏提纯塔、纯水蒸馏塔、半导体工业用扩散管、试剂提纯设备、蒸发器等;第二类是石英玻璃器皿容器。品种和规格有几百种,用途很广,从化验室到半导体集成电路生产都要大量使用。第三类是石英玻璃型材,有板、片、法兰、棒、棍、杆等,主要用于大型芯片加工的单片机石英材料、光刻基片、光电显示器板、光纤拉丝用支撑杆等。石英玻璃器件产品占石英玻璃工业总产值的1/3以上。近年来石英玻璃行业在生产工艺技术装备,质量都有极大的提高。在石英玻璃器件加工方面有突出进步,在发展太阳能电池用石英器件方面有突破性进展,受到国内生产太阳能电池的大型企业、公司等先进企业确认,生产的石英器件完全满足要求,产品质量已达到国际先进水平。从相关产业的发展来看,我国石英玻璃仍将保持年平均15%~20%的增长速度。信息产业用石英玻璃的增长速度仍大于电光源用石英玻璃。
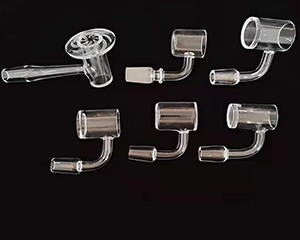
潮州市定制紫外线消毒灯厂家
装填氧化剂、还原剂、清灰和取出失效的催化剂(结块的氧化铜我们提供一手钻工具操作)时,需小心操作,勿碰撞石英管。装内封的管塞,密封圈上可涂一点高真空润滑脂(涂多了碳空白会高),装入时管塞与管口要垂直对正,缓慢旋转插入,取出时也应如此操作,否则易造成管子崩口。反应管装入仪器时应清除管上所有指印,避免形成结晶区域而引起石英过早老化。
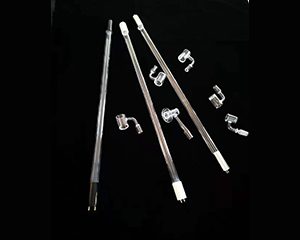
潮州市定制紫外线消毒灯厂家
多晶硅和石英玻璃的联合制备法的热能是被充分利用的,其生产过程没有反复升降温的现象,因此可以节能,而且节能的数字是相当可观的。采用传统的单项生产法生产多晶硅,还原料从鼓泡器里出来后被送进还原炉。在炉内还原料被加热到1150~1250℃,发生了氢还原反应,生成多晶硅。采用这种生产法,进入还原炉的还原料只有少数(一般认为10%~20%)参加反应,生成了多晶硅,绝大多数被当作尾气排放了。初,这些尾气被当成废气放掉,造成极大的浪费。为避免浪费,人们把尾气中的氢气和四氯化硅回收,经净化提纯后再利用。这样一来,出来的高温料,进入由冷冻分离器和氢气回收组成的回收系统回收。在回收系统里,还原料被冷冻降温至四氯化硅的沸点(57.6。C)之下,一般认为应在40~38℃为好。如按还原料在还原炉里的低限温度1150℃,降温后的上限温度40。C计算,也要降温1100℃。问题是,回收后4()℃的常温还原料要重新被送入鼓泡器里,然后通进还原炉,再次被加热到11501250。C的高温。从上述工艺中可以看出,进入还原炉被加热的大部分还原料(占进炉料9()%)没有被利用就被送出降温,而且降温后又被重新送入还原炉成为参加新一轮反应的还原料。很明显,这是一种浪费,没有参加反应的还原料按理说应该不加热。可问题是,在还原炉里,没有参加反应的还原料与参加反应的还原料是混在一起的,根本无法分开,如果没有参加反应的还原料不加热,那么,参加反应的还原料也无法加热。我们知道,参加反应的还原料温度低是无法进行化学反应的,也就无法生产出多晶硅。所以,如果采用传统的单项生产法生产多晶硅的话,上述浪费是不可避免的。